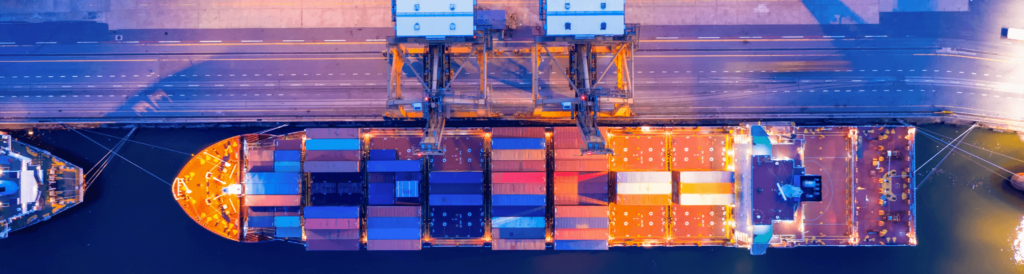
Kearney’s Reshoring Index makes it clear — a large majority of American companies have, or plan to, move some production from China to the United States in the next three years. As many as 80% of corporations have already made a move, often employing a supply chain design solution or experts to provide a deeper look into possible options.
To take a few recent examples of the changing offshoring tides:
- In January 2022, General Motors announced a $7-billion investment in four Michigan plants. The company, which makes Chevrolet, GMC, Cadillac, and Hummer vehicles, also said it spent almost $40 billion in 2021 on parts from 5,600 US suppliers.
- GE Appliances has invested more than $2 billion in its US plants and distribution centers since 2016 to bring products closer to customers and create more American jobs.
- Saying “America lost ground” in semiconductor manufacturing, Intel has poured $12 billion into two chip factories near Phoenix, Ariz., scheduled to open in 2024.
- Generac Power Systems has unveiled plans to open a new plant in Trenton, S.C., shortly after moving some production out of China.
- U.S. Steel is spending $3 billion to build a steelmaking factory in Osceola, Ark.
Before changing strategies, companies often look to supply chain design solutions, like GAINS, to provide the answers to how the various strategies would perform and the risks involved. The answer is rarely straightforward and includes many variables and data sets that need advanced analytics. The GAINS solution and team of supply chain designers have helped many companies evaluate their offshoring and nearshoring strategies and helped them discover the path that aligns with their approach.
But, to see how we got here and what has led us to these complex decisions, let’s explore the history of offshoring.
Offshoring Timeline: A Look Back at What Happened
Turn back time to the late 1970s; another trend was brewing — offshoring. Back then, Jack Welch, then CEO of General Electric, argued companies should move production wherever is cheapest to maximize profits and lower costs. GE offshored most of its manufacturing, as did its part suppliers, who were told to “migrate or be out of business.”
Over the next few decades, the offshoring race was on. And soon, the broader implications of production relocation were felt across the United States.
1990s: China Becomes Manufacturing Magnet
Throughout the 1990s, offshoring expanded rapidly, with companies increasingly shifting manufacturing operations to countries like China, India, and Mexico. China emerged as a dominant offshoring destination due to its large labor force, low production costs, and favorable government policies. Industries such as textiles, electronics, and automotive heavily relied on offshoring to optimize costs and tap into emerging markets.
Early 2000s: No End in Sight
By the early 2000s, offshoring continued to grow, fueled by cost savings and access to expanding consumer markets. At the same time, the debate over American jobs lost intensified, although the actual number remained unclear as no government agency kept an official tally.
Mid-2000s: Cost-Effectiveness Questioned
In the mid-2000s, concerns over rising labor costs and supply chain complexities became more prominent. Companies faced pressure to compete on price and deliver products faster in a globalized marketplace. Rising transportation costs and logistical difficulties started affecting the cost-effectiveness of offshoring.
Mid-2010s: Amazon Effect Sets In
In 2015, the mood was still glum in certain quarters. “Why aren’t U.S. corporations hiring?” The Week queried and replied, “Actually, many of them are. They’re just not hiring Americans.” While the Wall Street meltdown had shrunk U.S. payrolls by a net 500,000 jobs, the article noted that American corporations added 729,000 workers overseas.
But a trend shift was already underway. In 2012, for instance, Apple announced it was moving some overseas production of the Mac home in what some suggested was more than “post-crash green shoots…but a genuine shift back” to the U.S.
Throughout the 2010s, the era of Amazon Prime set the tone for the rapid growth of e-commerce and changing consumer expectations that put a greater emphasis on speed to market and responsiveness. Companies struggled to meet evolving consumer demands and deliver products quickly due to the distance and time associated with offshored production. Quality control, sustainability, and local sourcing also gained prominence, encouraging companies to reassess their offshoring strategies.
Late 2010s: Undeniable Losses Despite Trend Shift
By 2019, the Bureau of Labor Statistics had the data everyone had been looking for decades earlier — and it told the story of significant employment losses to offshoring in nondurable goods manufacturing industries from 1990 to 2019.
Apparel and textile products suffered the most considerable job losses, while printing and publishing added the most jobs. In relative terms, the apparel and textile industries lost 81% of jobs during this time.
2020s: Pandemic Upheaval Upends Supply Chain Priorities
Then, in 2020, came one of the biggest deterrents to offshoring to date. The COVID-19 pandemic exposed vulnerabilities in global supply chains, causing widespread disruptions. As McKinsey notes, supply chain resilience and agility became top priorities as companies sought to diversify sourcing strategies and reduce dependence on distant suppliers. Nearshoring and reshoring gained momentum, driven by the need for shorter supply chains, faster response times, and localized production to mitigate risks and better serve local markets.
Now: Combining Strategies for Enhanced Resilience
Today, companies are adopting a more strategic approach to global supply chain management, considering combining strategies, including offshoring, nearshoring, and reshoring based on specific product requirements, service needs, and market dynamics.
Using supply chain design, companies can build more agile and resilient supply chain networks, enabling companies to have the flexibility to manage disruptions and changing customer expectations. This network optimization from supply chain design uses factors such as proximity to innovation centers, sustainability, and ethical considerations to prioritize sustainability, control costs, improve service, and be more resilient regarding supply chain decisions about offshoring and much more.
Contact GAINS
Does your organization need the help of supply chain design experts, backed by the latest supply chain planning software, to navigate new acquisitions or organic growth? With a 97% customer retention rate, we build on a history of delivering rapid results. Contact GAINS and start a conversation today.