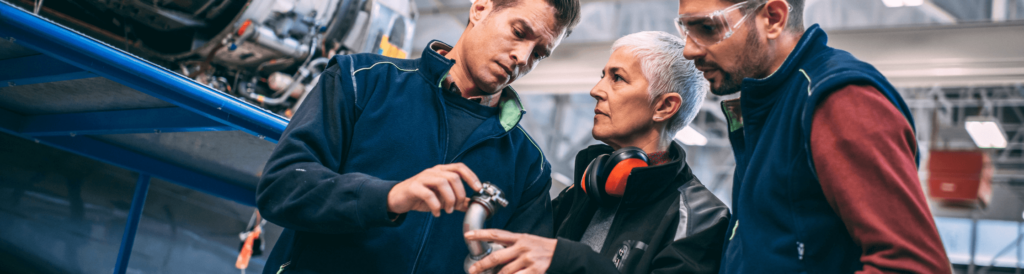
Behind the scenes in the service parts or MRO industry is a complex web of supply chain management challenges
Maintenance and repair organizations are indispensable to many companies. They are integral in keeping machinery and equipment operational to keep costs under control and make customers happy. Maintenance, Repair, and Operations (MRO) services are vital; companies that rely on complex machinery, equipment, or vehicles for their core operations often depend on MRO services to keep the business going. GAINS works with MRO businesses across industries and types to ensure that they can keep those machines up and running!
Types of MRO Organizations:
In-House: Many large corporations have internal MRO departments responsible for maintaining their equipment.
Third-Party: These are specialized companies that provide MRO services to other businesses.
OEM-Managed: Original Equipment Manufacturers (OEMs) may also offer MRO services for the products they produce.
Let’s look at some pressing issues MROs face and how a solution like GAINS supply chain planning can make a difference.
7 Common Supply Chain Challenges of the MRO Industry
1. Parts Availability:
- Challenge: The availability of specific parts for the aviation industry, for example, can be critical to maintaining operational schedules. Running into scarcity issues means delays and downtime for aircraft, leading to dissatisfaction and potential revenue loss for aviation companies.
- Recommendation: Implementing robust inventory tracking systems and engaging in strategic relationships with multiple suppliers can minimize this issue. Collaborative forecasting and demand planning can also help avoid unexpected spare part shortages.
- GAINS Solution:
- Real-Time Visibility: GAINS provides real-time insights into inventory levels across multiple locations, allowing for efficient tracking and management of stock. When problems arise, you will know in advance and be able to enact proactive solutions to minimize downtime.
2. Inventory Management:
- Challenge: Managing inventory is a complex balancing act. Excessive stock leads to high carrying costs, while shortages can cause operational delays.
- Recommendation: Implementing advanced inventory systems and utilizing analytics to right-size inventory planning can minimize carrying costs and shortage risks.
- GAINS Solution:
- Optimization Algorithms – GAINS uses advanced algorithms to balance inventory levels, considering demand, lead time, and costs. This approach reduces overstocking and understocking, helping to minimize inventory-related issues and eliminate expediting.
3. Technology Integration:
- Challenges: Lack of unified technology across the supply chain can lead to errors and inefficiencies, making coordination tricky.
- Recommendation: Investing in integrated systems and platforms that enable real-time tracking and analytics can streamline operations and boost efficiency.
- GAINS Solution:
- Integration with Existing Systems: GAINS can be integrated with existing ERP or other enterprise systems, creating a seamless flow of information across the entire supply chain.
- Scalability: Whether a small business or a large enterprise, GAINS can be scaled to fit the specific needs and complexities of the company.
4. Obsolescence Management:
- Challenges: In aviation and other MRO sectors, obsolete parts must be managed and replaced efficiently.
- Recommendation: Regular audits and having strategic partnerships with suppliers specializing in specific legacy parts can help manage obsolescence effectively.
- GAINS Solution:
- Collaborative Planning: The platform allows input and collaboration between departments, such as sales, marketing, and operations. Ensuring a more cohesive approach to inventory planning. If a replacement part is shared between more than one piece of equipment, you can ensure that GAINS will track its usage and report it to all stakeholders if the part needs reordering.
5. Supplier Relationships:
- Challenges: A single supplier’s delay (or shutdown) can disrupt the entire supply chain, causing delays and cost overruns.
- Recommendation: Building solid relationships with suppliers, diversifying the supplier base, and including contractual agreements about supplier performance that ensure timely delivery can mitigate this risk.
- GAINS Solution:
- Supplier Collaboration: GAINS enables supplier collaboration through shared forecasts, order commitments, and other information. This collaboration ensures better alignment with supplier capabilities and can lead to stronger relationships.
- Risk Mitigation: GAINS allows for risk analysis and mitigation by integrating data from multiple suppliers. If a problem arises with one supplier, alternatives can quickly be identified.
6. Demand Forecasting:
- Challenges: The unpredictable nature of the MRO field makes demand forecasting very difficult, often leading to overstock or understock scenarios.
- Recommendation: Employing sophisticated forecasting models that consider various factors, including seasonal trends and historical data, can lead to more accurate predictions.
- GAINS Solution:
- Responsiveness to Changes: GAINS can adapt to sudden changes in demand or supply, providing insights and recommendations on how to respond. This agility helps in avoiding unexpected shortages.
- Optimized demand plans: We help planners to define strategies derived from automated multi-echelon modeling based on item demand history, point of sale data, machine/fleet usage, leading indicators, and Sales & Operations Planning (S&OP) data.
7. Cost Control:
- Challenges: Fluctuating commodity prices and other variable costs can make cost control a continuous battle.
- Recommendation: Implementing cost-tracking systems, strategic sourcing, and ongoing supplier negotiations can help maintain control over costs.
- GAINS Solution:
- Reducing Holding Costs: By accurately forecasting demand and aligning it with inventory levels, companies can avoid overstocking, which results in holding costs.
- Automating Processes: Automation can reduce labor costs and enhance accuracy, minimizing errors that lead to costly corrections.
- Risk Mitigation: Effective design includes risk assessment and mitigation strategies that can prevent costly disruptions.
Conclusion
The inventory challenges in the MRO industry are substantial, but as highlighted above, they also offer opportunities for innovation and optimization. By employing a Supply Chain Planning and Design solution like GAINS, MROs can transform these challenges into competitive advantages. Leveraging technology and adopting best practices to address these problems leads to greater efficiency, responsiveness, and profitability.
MRO companies can innovate, streamline operations, and thrive in a competitive marketplace by viewing these challenges as opportunities.
Learn More about GAINS can help you streamline your supply chain, optimize inventory management, and drive efficiency within your organization by contacting our expert team or scheduling a personalized demo today.