Customer Success
QubicaAMF Success with GAINS
Growing market share through industry leading customer service using the power of GAINS inventory planning and profit optimization
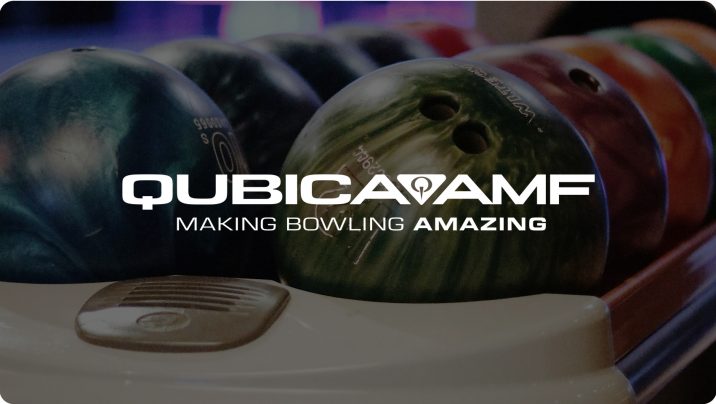
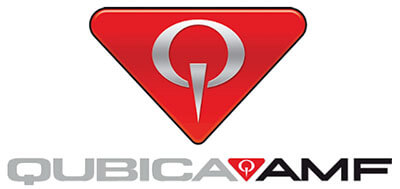
- The largest bowling products company in the world
- Headquartered in Richmond, Virginia and in Bologna, Italy
- Serve and support more than 10,000 centers in 90 countries
- Maintains the industry’s largest R&D team for electro-mechanical products, software, electronics and entertainment systems
- ERP: JDE
$150
thousand in annual savings due to increased visibility and improved sourcing decisions
95%
customer service level, exceeding company targets
11%
improvement in manufacturing labor utilization
95%
off-the-shelf availability of all products
$75
thousand in savings on freight expenses in the first year
Company Overview
QubicaAMF is the largest and most innovative bowling equipment provider in the world with 100 years of experience and an ongoing mission of “Making Bowling Amazing.” In June 2005 industry leaders AMF Bowling Products and Italian-based Qubica S.p.A announced that they would join forces. The result of this strategic alliance, QubicaAMF Worldwide, became one of the largest manufacturers of bowling and amusement products in the world.
“The GAINS project provided the greatest corporate ROl of any IT project in the history of the company.”
President and CEO QubicaAMF
Challenges
Considering the inherent complexities that arise post-merger, QubicaAMF realized fundamental changes were needed to efficiently manage their supply chain as a platform for more profitable growth. With a goal to improve fill rates while reducing excess inventory, the QubicaAMF team selected GAINS, confident the robust platform would help achieve a cost-effective 95% off-the-shelf-availability of all products. Additionally, QubicaAMF identified an opportunity to synchronize inventory investments and lower overall operating costs.
Objectives
Positive they had found the right partner in GAINS, QubicaAMF set out to transform their global supply chain. Serving more than 10,000 bowling and entertainment centers in over 90 countries, QubicaAMF utilizes a worldwide sales and distribution network. GAINS was able to fundamentally change and improve every aspect of their supply chain planning and operations process. Beyond meeting inventory improvement and fill rate goals, QubicaAMF also realized an 11% improvement in labor utilization in their manufacturing division. The boost in labor efficiency was a direct result of both automated inventory management and the optimized scheduling. GAINS also optimized purchased lot sizes allowing QubicaAMF to renegotiate vendor agreements resulting in more than $150,000 in savings annually.
- Reduce inventory while improving order fill rates
- Ensure off-the-shelf availability of all products
- Develop best-in-class customer service levels