Service Parts and MRO
High-impact results for complex service parts supply chains.
Service parts companies are familiar with long lead times, high cost parts, multiple sources for the same part, sporadic and low-volume part usage patterns, and requirements/ preferences of OEM vs PMA parts. GAINS is built to conquer these challenges, providing the supply chain optimization capabilities service parts and MRO (maintenance, repair and operations) organizations need to avoid misaligned inventory.
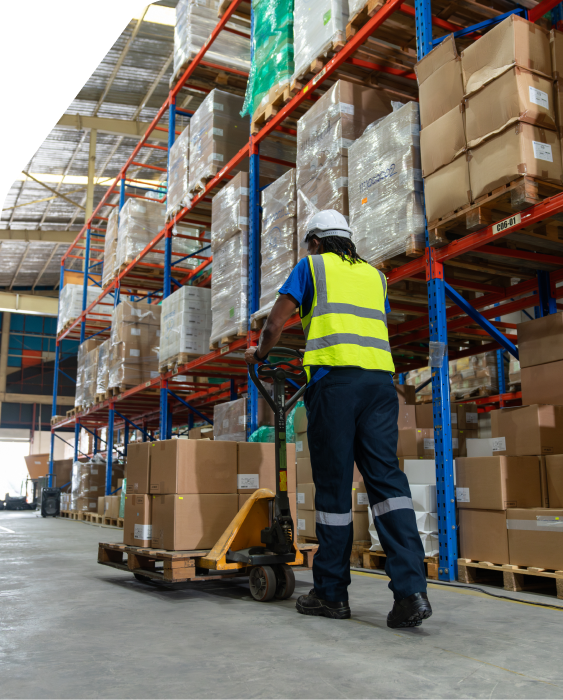
Turn supply chain chaos into clarity.
Reduce Inventory
GAINS empowers parts and MRO companies to reduce inventory by providing real-time visibility into demand patterns, production schedules, and supplier performance. In a market environment with rising interest rates and inflation, the lean inventory management practices powered by GAINS are vital for businesses seeking to lower storage costs and improve access to working capital.
15-32%
Reduce Inventory
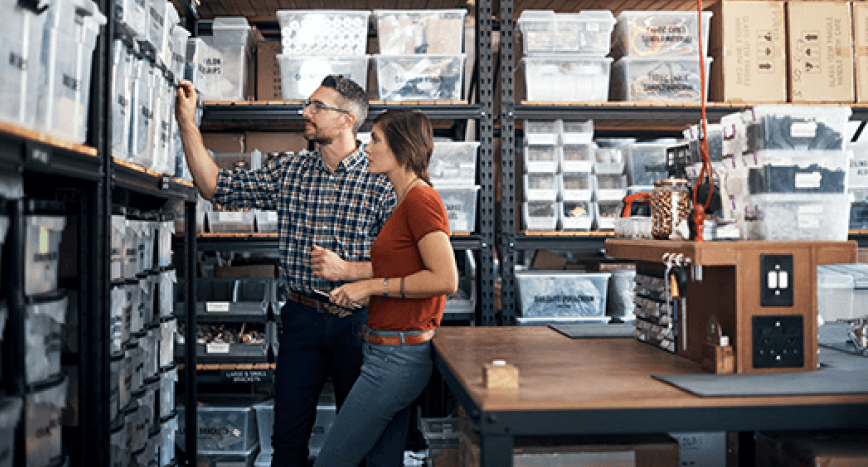
Lower Operating Costs
Advanced capabilities like independent demand forecasting, item supersession, inventory classification, BOM planning, and part/repair process optimization help your team meet requirements on budget and on time. They also ensure repair parts inventory is right-sized to meet demand, resulting in lower operating costs.
12-30%
Lower Operating Costs
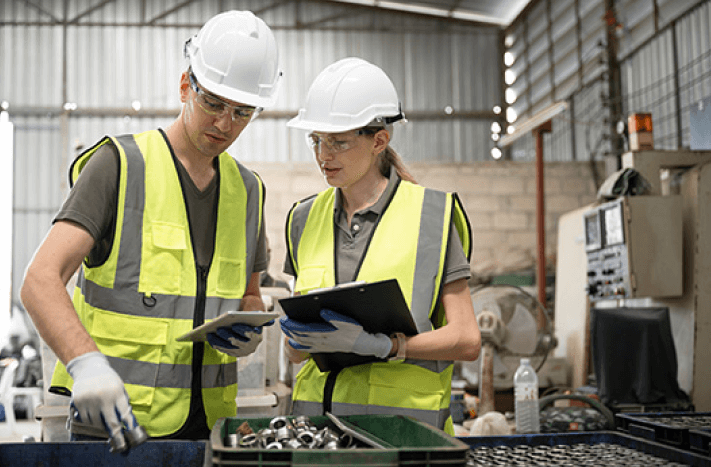
Increase Sales
GAINS gives your supply chain team the ability to assess demand patterns, inventory levels, and production capacity. It even recommends the most efficient replenishment strategy. This enables your company to keep up with parts demand and improve sales performance.
5-20%
Increase Sales
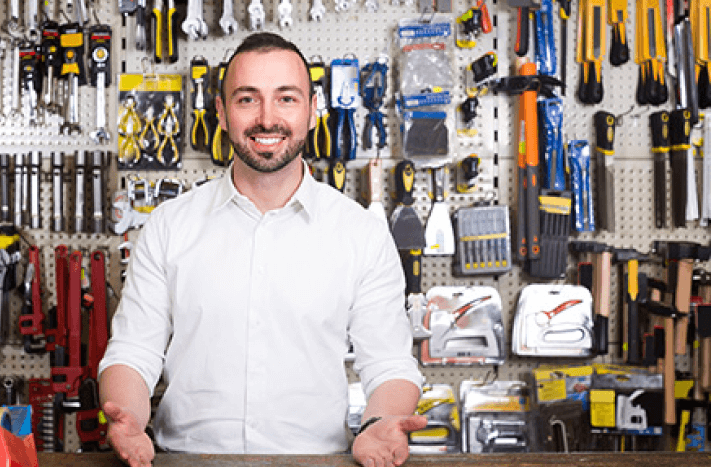
Boost Service Levels
GAINS gives parts and MRO companies clear insight into exceptions and deviations from the normal flow of operations. By signaling potential issues such as stockouts, late deliveries, or quality issues, your team can proactively address concerns and maintain consistent service levels. Insights into customer behaviors, preferences, and buying patterns empower you to improve product assortment to enhance sales performance.
96%
Increase Service Levels
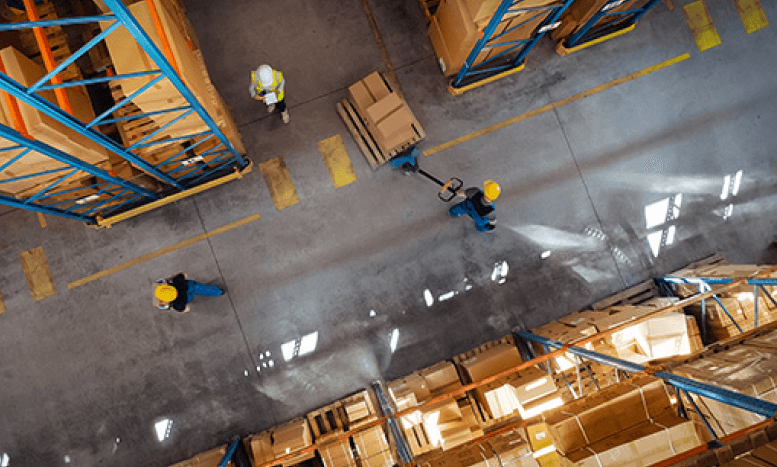
GAINS informs or automates millions of supply chain decisions a day.

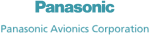
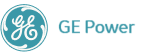
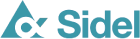


Key Capabilities
Multi-channel fulfillment planning
Dynamically optimize supply planning into the supply/DC network supporting the retail locations, which includes multi-channel fulfillment planning.
Scalable, multi-tier optimization
Methods that consider a comprehensive set of parameters, costs, and margins across the enterprise.
Store-level inventory optimization
Ensure maximum profit (minimum cost) is achieved considering the comprehensive set of costs (e.g. transportation, handling, holding, expiration, etc.).
Item deployment and service level policy optimization
Ensure maximum profit or minimum cost is achieved considering a comprehensive set of costs including: carrying, handling, obsolescence, and transportation.
Purpose-built functions
Address common challenges prevalent in the MRO sector specifically, such as sporadic and low-volume part usage, and ensuring service part availability.
Dynamic inventory re-distribution
Designed for condition-based supply planning to ensure targeted service level is sustained at least cost.
Fully-integrated
Comprehensive multi-echelon planning solution to run the entire MRO supply chain from one place.
Compatible with any ERP
Whether your organization has one or multiple ERP systems, or even homegrown spreadsheets, integration with GAINS is data-agnostic, and is SAP and Oracle Certified.
Explore other solutions
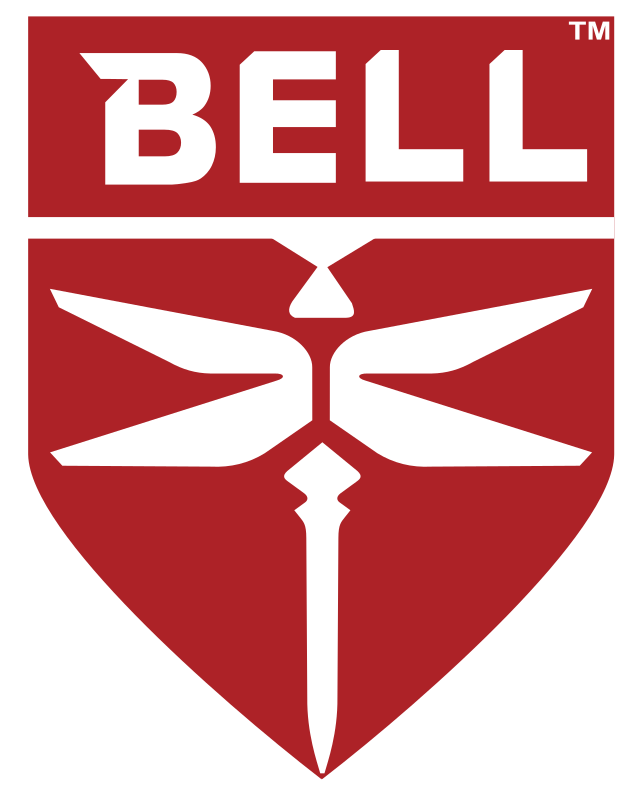
With GAINS, we are able to provide the best service in the industry with 19% less inventory and 30% lower handling costs.
Manager, Support Systems Development
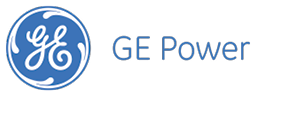
When providing repair and maintenance to electric power generation facilities, part availability is a given. GAINS made sure we always had parts on the shelf so no system was out of service; yet we still reduced our inventory investment and operating costs by over 25%.
Director, Materials Management
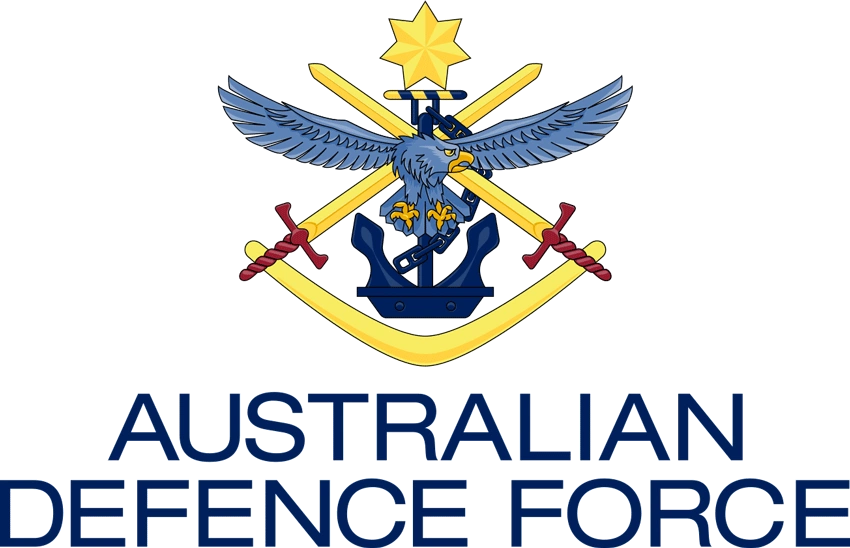
We saved $14 million in six months. We are often promised these kinds of numbers; we’re just not used to having them delivered, GAINSystems, beyond a doubt, delivered.
Wing Commander
Related Resources
Imagine if your procurement team knew when commodity prices would surge? Your enterprise would lock [...]