MEIO
GAINS Multi-Echelon Inventory Optimization (MEIO) for ERP
Move beyond Inventory Optimization and Unlock the ability to optimize stock levels across the entire value chain. Complex supply chains need MEIO solutions for their inventory optimization for overall orchestration.
Every SKU matters.
Generate optimal inventory targets across the entire value chain.
Our multi-echelon inventory optimization plugin can seamlessly sit above other APS solutions to ingest transaction, stocking strategy, and business roles. GAINS’ MEIO automatically cleanses data and creates an inventory optimization plan at the SKU level. Our sophisticated analytics are used to calculate the optimal inventory levels at multiple locations while considering uncertainties in demand and forecasts, supply, and lead time. Results are then fed back into the APS environment where the execution of stock parameter changes occur.
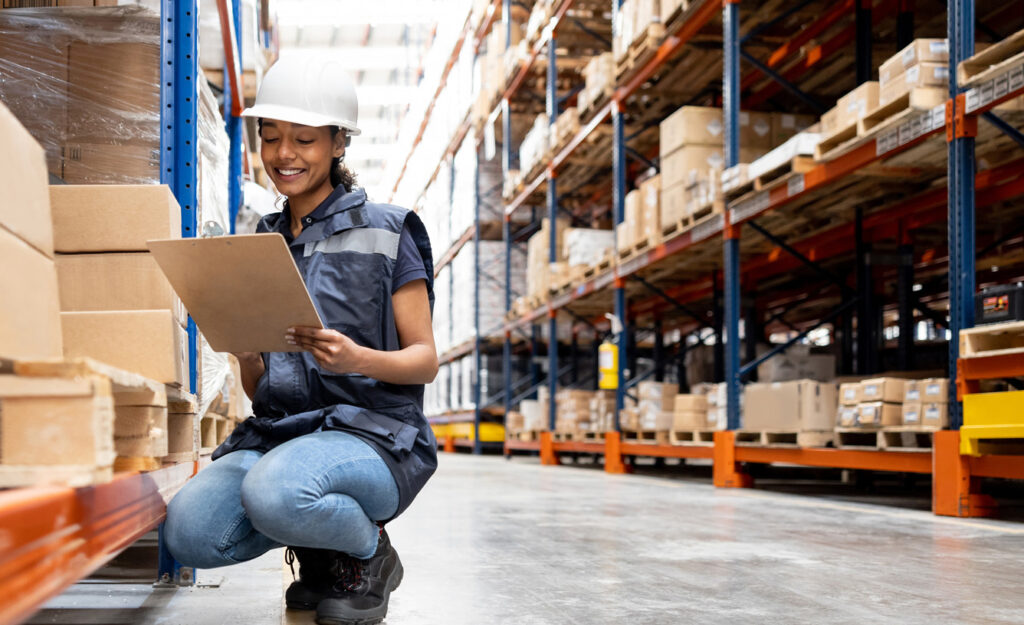
Move beyond inventory optimization.
Inventory optimization (IO) sets stock levels at individual supply chain points, while multi-echelon inventory optimization (MEIO) optimizes inventory across the entire value chain simultaneously. MEIO is particularly beneficial for complex supply chains, providing a comprehensive view of demand forecasts and suggesting optimal stock levels at each stage for more efficient management.
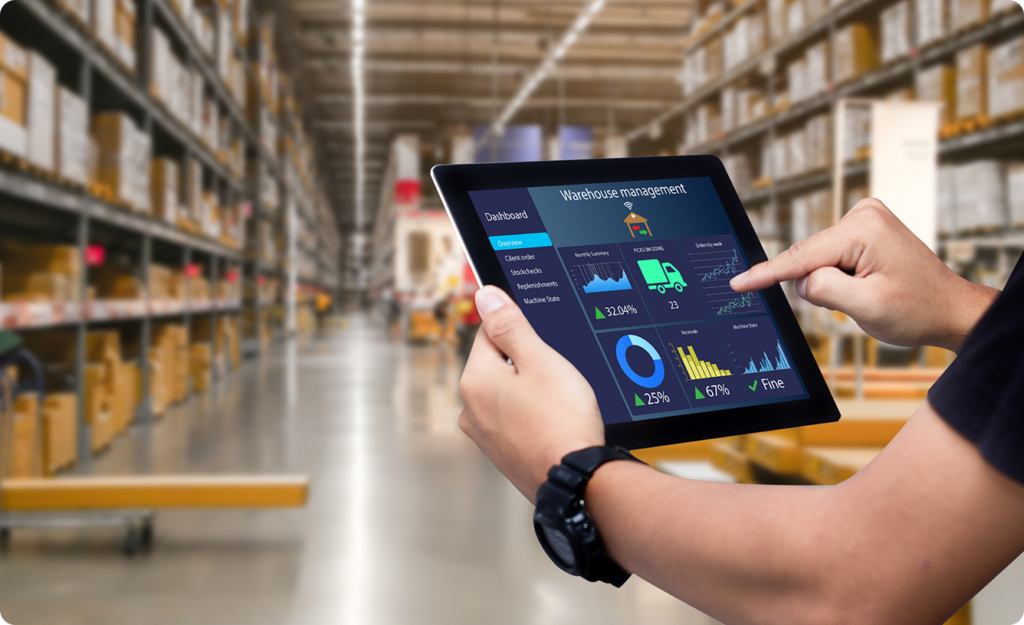
Maximize supply chain performance.
MEIO offers a comprehensive approach to supply chain management, optimizing inventory across multiple locations by considering historical data and future impacts. While not a cure-all, it provides a holistic framework that may necessitate changes in roles, responsibilities, and performance metrics throughout the organization.
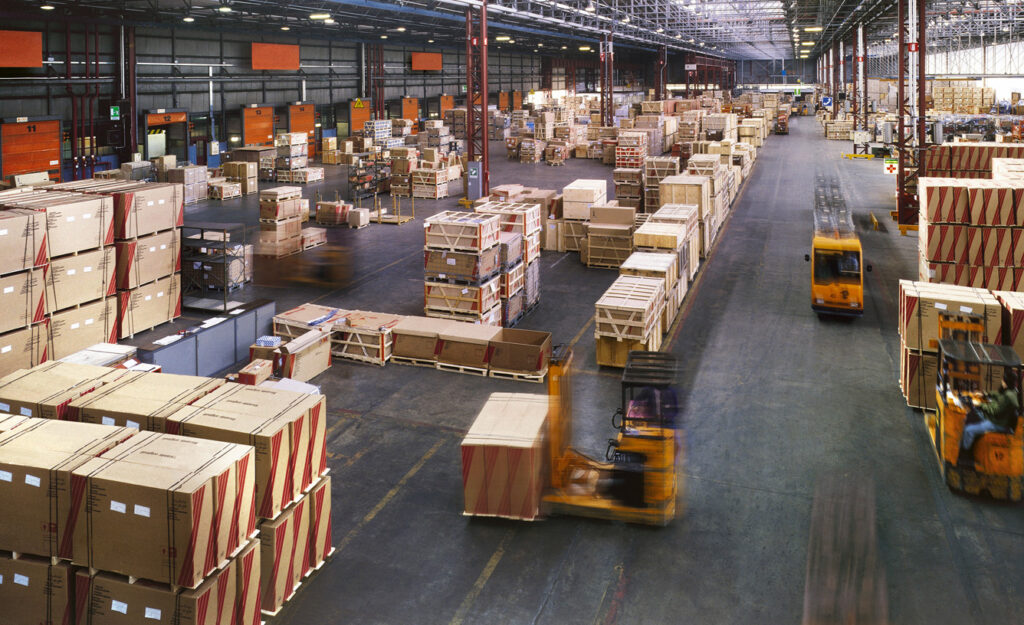
Core Features: what’s included
Multi-echelon stocking policies
Determine whether or not to stock an item and at what service level, solving for interdependencies within a BOM or distribution network.
Automated multi-echelon modeling
Dynamically determine the profit-optimal stocking strategy for each SKU in the BOM.
Inventory policy optimization
Precisely achieve targeted service levels by comprehensively managing sources of variability.
Service level optimization
Automatically determine service levels uniquely for each item to achieve an aggregate target while achieving the business objective.
Learn more of DEO
Frequently asked questions
How does GAINS software help supply chain managers in reducing inventory carrying costs?
GAINS software provides powerful tools and insights that help supply chain managers reduce inventory carrying costs through a combination of advanced analytics, real-time data, and strategic optimization techniques. Here’s how:
- Demand Forecasting Accuracy: GAINS improves demand forecasting accuracy by leveraging advanced analytics and AI. This ensures that inventory levels align with actual demand, reducing excess stock and minimizing carrying costs.
- Dynamic Safety Stock Management: Our software dynamically adjusts safety stock levels to ensure you have the right amount of buffer stock to manage all of the sources of variability in your supply chain. This optimizes inventory buffers, preventing overstocking while ensuring sufficient supply to meet customer needs.
- Network-Wide Inventory Visibility: GAINS provides real-time visibility into inventory levels across the entire supply chain. This allows managers to make informed decisions about stock transfers, reordering, and demand fulfillment, reducing unnecessary inventory buildup.
- Optimized Replenishment Strategies: We implement optimized replenishment strategies that consider lead times, order quantities, and supplier reliability. This ensures timely restocking with minimal inventory holding, reducing carrying costs.
- Advanced Inventory Segmentation: GAINS software segments inventory based on various criteria, including demand patterns, product lifecycle, and profitability. This targeted approach helps prioritize high-value items and manage slow-moving stock more effectively.
- Continuous Monitoring and Alerts: Our software continuously monitors inventory levels and provides alerts and recommended actions for potential issues such as stockouts or excess. This proactive approach enables timely interventions to maintain optimal inventory levels.
- Scenario Analysis and Simulation: GAINS allows managers to perform scenario analysis and simulations to understand the impact of different inventory strategies. This helps identify the most cost-effective approaches to inventory management.
- Collaboration and Integration: Our software integrates seamlessly with other systems and promotes collaboration across departments. This ensures that inventory decisions are aligned with overall business objectives and operational constraints.
Can GAINS optimize inventory across a global supply chain with varying lead times and service requirements?
- Global Visibility: GAINS provides comprehensive visibility into inventory levels down to individual SKUs by location (SKUL) and movements across all locations in your supply chain. This real-time insight enables better coordination and informed decision-making to optimize inventory distribution.
- Advanced Analytics: Our advanced analytics tools account for the complexities of global supply chains, including varied lead times, transportation modes, and demand variations by region. This allows supply chain professionals to create precise and efficient inventory strategies.
- Lead Time Management: GAINS accurately models lead time variance across different suppliers and regions. Incorporating these lead times into our algorithms ensures that inventory levels stay balanced and aligned with service requirements.
- Service Level Optimization: We optimize inventory levels for all markets and products to meet your specific service requirements. This ensures high service levels and customer satisfaction while right-sizing inventory and carrying costs.
- Dynamic Replenishment: GAINS implements dynamic replenishment strategies that adapt to changes in demand and supply conditions. This flexibility ensures timely restocking and reduces the risk of stockouts or overstock situations.
- Scenario Planning and Simulation: Our software allows for scenario planning and simulations to evaluate the impact of various factors on your inventory performance. This helps to develop robust strategies to manage uncertainties and disruptions in the global supply chain.
- Integrated Supply Chain Solutions: GAINS Connect integrates seamlessly with other supply chain management systems, ensuring smooth data flow and collaboration across your supply operation. This holistic approach enhances overall supply chain efficiency.
- Continuous Improvement: We continuously monitor and analyze inventory performance, providing insights and recommendations for ongoing optimization. This commitment to continuous improvement ensures that your inventory strategies remain effective amid continual uncertainty.