Traditional demand forecasting methods rely on historical data alone, leaving your company vulnerable to the whims of the market. Demand sensing works alongside your existing supply chain planning processes to improve forecast accuracy and operational efficiency.
Learn about demand sensing and advanced forecasting from the supply chain optimization experts at GAINS.
What Is Demand Sensing?
Long-established demand planning processes rely heavily on historical sales data, assuming stable future demand levels. With rapidly shifting consumer preferences, nonlinear supply chains, and unexpected disruptions aplenty, today’s markets are not so predictable. Modern demand sensing leverages AI technology, advanced analytics, and real-time data to better plan for sudden shifts in demand.
So far, we’ve used two different terms for how supply chain professionals make decisions with demand in mind, but what is the difference between demand planning and demand sensing? Though the terms are similar and often confused, demand planning refers to the overall process in which demand sensing plays an important role — it supplies the information used to make actionable plans on inventory stocking and product distribution.
Demand Sensing vs. Demand Forecasting: When to Use Them or Lose Them
Two equally often confused terms, “demand sensing” and “demand forecasting,” fulfill the same role in the overall demand planning process. However, each uses different methods and works better for different time frames. Demand sensing focuses on real-time data, making it ideal for short- to mid-term forecasts. Conversely, demand forecasting focuses on long-term historical patterns in demand to plan further into the future.
For example, demand forecasting would be the better method for predicting seasonal shifts in demand that reliably repeat each year. On the other hand, demand sensing might help companies adapt more agilely when something unexpected pops up, like an upcoming event driving new interest in their products.
Importance of Demand Sensing in Supply Chain Management
With unlimited access to information, consumer preferences are constantly evolving. An influencer might mention a company’s product one day and cause demand to skyrocket the next.
Consider the Stanley Cup, which rapidly rose in popularity over the past year despite existing for over 100 years. After a clip of the product went viral on TikTok, retailers were rarely able to keep Stanley Cups on their shelves without total pandemonium setting in.
While the Stanley Cup is an extreme example of the need for demand sensing, companies of every size can benefit from more accurately predicting shifts in demand. Benefits of demand sensing include:
- Better matching your product mix to actual demand, enabling you to meet customers’ expected service levels consistently
- Reducing the need for sudden changes in your production schedules and emergency shipments with exorbitant costs
- Capitalizing on rapid upward swings in demand by having enough product to meet the opportunity, increasing your revenue
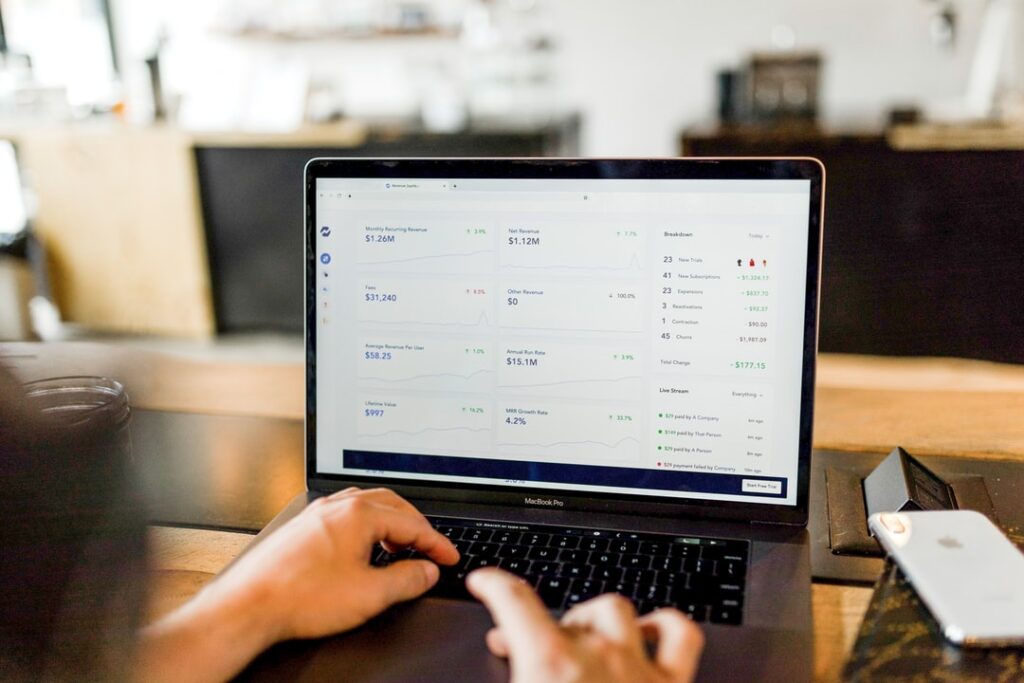
Demand Sensing in Supply Chain: How Does It Work?
When implementing demand sensing into your supply chain, consider the following five key components and two best practices.
Key Components of the Demand Sensing Process
The key aspects of demand sensing involve finding and using the right data to create and optimize models.
- Data Collection: Consider both historical and real-time sales data, as well as customer input. Include external data about events, trends, economic indicators, weather patterns, traffic, and more.
- Data Integration: You must clean and standardize all data so it’s usable and makes sense when combined. Internal and external sources often provide information in various incompatible formats, making this step tricky. Ease this effort by using the right software mix and collaborating with supply chain data experts.
- Data Analysis: After uploading data to your processing system, set up both statistical and machine-learning algorithms to find key patterns in the data that traditional methods might miss.
- Modeling Techniques: After your initial analysis, use your findings to build models that predict future demand for the product in question with greater accuracy.
- Optimization Strategies: Use demand sensing insights to create and execute actionable plans for improving your company’s supply chain and production processes. Achieve cost savings by reducing excess inventory and stockouts with better data-backed decisions.
Best Practices for Demand Sensing Implementation
When implementing a demand sensing plan, we advise:
- Finding the Right Fit: Use the right tech stack to make data aggregation, integration, and blending easy. The last thing you want is to be stuck in a months-long implementation where, in the end, the product doesn’t work well for your professionals. When shopping around for the right system, ask about implementation, integration with existing tools, and ongoing support to find software that enhances your processes rather than complicating them.
- Updating Models Regularly: A predictive model isn’t a “set-it-and-forget-it” tool. As new data becomes available, incorporate it to improve demand forecasting accuracy. The model will provide more accurate forecasts using machine-learning algorithms as it continuously learns from new data.
Technologies Driving Demand Sensing and Future Trends
Learn about the emerging technologies and techniques behind innovations in demand sensing.
Advanced Analytics
Rather than only using past data, demand sensing tools process both historical and real-time data so you can better visualize the smaller picture. With internal and external inputs, advanced analytics help you utilize larger volumes of information and sort out valuable patterns from the noise.
Machine Learning
Improving algorithms was more manual and tedious when using traditional forecasting methods. Machine learning (ML) technology powers advanced simulation modeling by discovering more about the nature of your product’s demand as time passes and the system accesses more data.
Artificial Intelligence
Artificial intelligence (AI) is built to parse out complex data in large volumes and turn it into something new and digestible. This makes it a particularly powerful tool to get a better idea of how demand might react to subtle or sudden shifts in the near future.
The Rise of Automation
Automation eliminates the need to focus on menial data collecting, cleansing, and management tasks. While some aspects of the demand sensing process still need a human touch, the right forecasting tool can automate repetitive and time-consuming elements like integrating and standardizing data from multiple sources.
Improve Demand Planning Accuracy With GAINSystems
At GAINS, the supply chain performance optimization company, we’re committed to helping you achieve better outcomes. Our demand planning and forecasting software helps you do just that through advanced analytics, AI, ML, and superior support. Embrace the future of supply chain management with better predictive tools from GAINS.