What is lean manufacturing and when was it created? The term “lean manufacturing,” first coined in 1988, has principles that reach as far back as the early 20th century.
Lean manufacturing, or lean production, is a philosophical approach that focuses on eliminating waste in every process to enhance operational efficiency and improve customer satisfaction. In simple terms, lean manufacturing helps companies optimize resources like their employees, materials, and inventory to make processes run smoothly.
Learn about the ideas behind lean manufacturing and discover functional tips for implementing this mindset into your company’s processes.
What Are the 5 Principles of Lean Manufacturing?
The 5 principles of lean manufacturing include value, the value stream, flow, pull and perfection. Within these:
- Value involves matching how much customers are willing to pay for a certain product or service quality.
- The value stream looks at mapping and optimizing all processes in the full lifecycle of the product.
- Flow means smoothing out any rough edges of transitions between tasks and lifecycle stages.
- Pull refers to a system where demand dictates production levels instead of internal goal setting.
- Perfection means that companies should constantly try to make continuous improvements to perfect processes.
Benefits of Lean Manufacturing
Lean manufacturing promotes many functional benefits, including enhanced operational efficiency, better quality of products that meets customers’ needs, and more.
Improved Efficiency
Idle workers, poorly planned processes, and excess materials drain your efficiency. Removing these issues to streamline systems makes production more productive.
Additionally, becoming energy-efficient can help you have a green supply chain, which makes your business more environmentally friendly while saving you additional money. Supply chain sustainability is a huge and growing concern for corporations and consumers alike, so making changes that limit your environmental impact can also appeal to customers.
Enhanced Quality
Understanding what customers want and using this information to make your products better is a key element of lean ideals. Specifically designing manufacturing operations with the consumer’s desired quality and service levels in mind makes your company more competitive.
Reduction of Operational Costs
Wasting time or money costs your business. Lean manufacturing helps you right-size inventory to avoid overpaying for storage. It also makes processes more efficient so you aren’t paying workers for idle time or “busy work.”
Increased Customer Satisfaction
Mapping the entire value stream and improving flow both translate into delivering the products and services your customers want more efficiently. This will improve consumer loyalty with your brand.
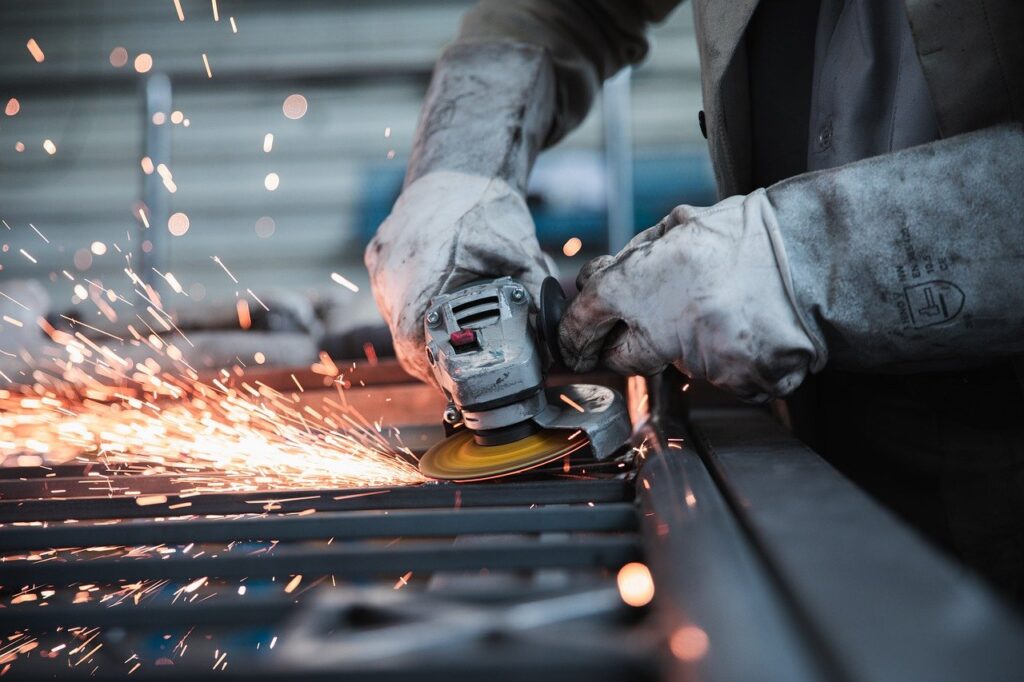
The Eight Types of Waste
Leaders in lean manufacturing like Toyota have identified eight distinct types of waste, including:
- Overproduction: Making more products than demand dictates can lead to wasted time and effort.
- Waiting time: Mismatched timing on concurrent or consecutive tasks means employees will waste time waiting before they can perform assigned work.
- Excess inventory: Keeping too many products on hand translates into wasted storage space and money.
- Defects: Fixing costly defects wastes both time and materials.
- Unused talent: Not using employees to their full potential results in wasted opportunities for efficiency and excellence.
- Transportation: Moving people, equipment, or materials more often or further than necessary wastes time, money, and effort.
- Motion: Extra movement by people that doesn’t add any value to production can cause workers to become tired, overworked, or even injured — wasting both time and people resources.
- Extra processing: When unnecessary features are added onto a product that consumers don’t actually want, this can be a waste of time and materials used to create these features.
Tips To Implement a Lean Manufacturing Process
When implementing a lean manufacturing mindset and relevant practices to your company, prioritize:
- Incorporating lean manufacturing as a philosophy that can be customized to fit your company’s unique needs, not a standardized set of processes that will work for every company equally.
- Focusing on applying the underlying principles of lean manufacturing to improve your existing processes rather than fully transforming operations at the outset.
- Continuously changing, monitoring, and assessing processes to keep aiming for the perfect set of procedures for your business.
- Breaking complex systems down into their simplest counterparts to assess their effectiveness and eliminate any waste.
- Encouraging every staff member at every level to participate in identifying and suggesting areas of improvement.
- Engaging personnel by educating them about the principles of lean manufacturing and how to apply them, rather than pushing changes on them without achieving buy-in first.
- Gathering feedback from employees on your lean manufacturing implementation along the way.
- Ideating and executing, since one doesn’t provide actual benefit to your business without the other.
- Putting in place reliable methods for measuring key operational metrics, so you can accurately decide whether a specific change has led to less waste, faster processes, or better quality.
Lean Manufacturing Tools and Techniques
The following theories and strategies can help you implement lean manufacturing principles efficiently.
- 5S Methodology: Helps workers sort, set in order, shine, standardize, and sustain their work spaces. This can have a significant impact on teams visualizing the benefits of lean principles and developing a continuous improvement culture.
- Value Stream Mapping (VSM): This strategy involves analyzing, designing, and managing the flow of products and information, from the raw material stage all the way to customer delivery. It helps companies have a full-picture view of their product’s lifecycle and eliminate waste to improve each stage.
- Kanban Systems: In the “just-in-time” (JIT) manufacturing system, Kanban handles inventory control. It shows how work progresses in each task of a process using colored cards. This visualization is used to limit the buildup of inventory in any one part of the production process, making sure each step receives only the materials it needs when it’s able to effectively use them.
- Root Cause Analysis (RCA): This technique discovers the initial, underlying cause behind each production problem to address it lastingly. Rather than treating the most obvious, surface-level symptoms of an issue quickly, companies use this method to dig deeper and diagnose issues to correct them properly in one go.
Improve Supply Chain and Manufacturing Efficiency With GAINSystems
There’s a reason GAINS is the supply chain performance optimization company of choice for brands like Honda, Safelite, Menards, and L’Oreal. Our manufacturing planning and optimization software combines advanced analytics, AI, and machine learning to accurately predict demand, eliminate process waste, and get the most out of every stage in your supply chain. Find out how incorporating GAINS into your tech stack can help you achieve savings, operational efficiencies, and enhanced customer satisfaction.